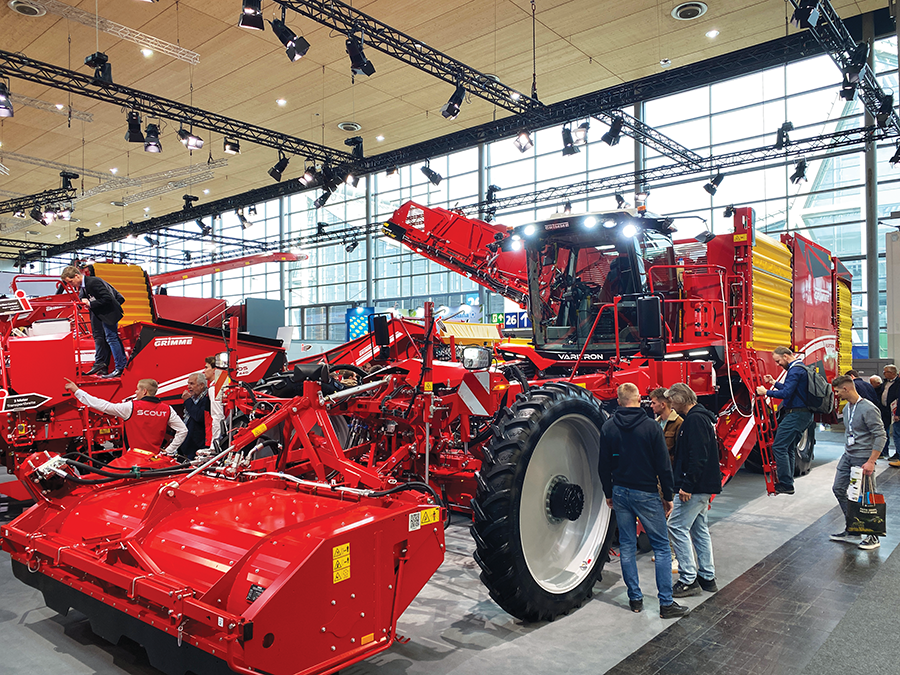
Potato growing advances take center stage at Agritechnica
Every two years, equipment manufacturers from around the world gather in Hanover, Germany for Agritechnica, the world’s largest trade fair for agricultural machinery. After a four-year lapse, the trade fair returned with renewed energy Nov. 12-18.
The fair’s host, the German Agricultural Society (DLG), presented 18 innovation awards this year, with three potato equipment manufacturers receiving a silver innovation honor.
PRIZE-WINNING POTATO INNOVATION
The three silver innovation awards were selected based on a product’s ability to significantly improve functionality and process, reduce workload or enhance work quality.
Rotating ridge former
German manufacturer ALL-IN-ONE GmbH won for its rotating ridge former. What makes the ridge former unique is its ability to work through tough residue in a variety of soil conditions.

The judges found that the shape of the rolling elements improved ridge formation in a way that allowed for enhanced air and water exchange within the soil.
High-tech windrower
Jointly developed by Shaktiman and Grimme, Spudnik’s sister company in Europe, a potato windrower with SmartFold technology won the second silver medal.
In many parts of the world, potatoes are cleared from the ground using simple, mounted, 2-row windrowers, in combination with a 40–70 horsepower tractor, and then picked up by hand. This method results in 5% to 20% harvest loss.
The new SGRW 200 is a mounted windrower with foldable second main web. The two-row machine is fitted with share blades commonly used in Europe. As it only clears the tuber nest in the ridge, it conveys much less soil into the machine.
The windrower’s design not only improves work quality but boosts capacity, making it a good fit for small- scale potato growers in developing countries where the quality of work during harvest is gaining importance.
Separation technology
Grimme won a second silver medal for ChangeSep, its interchangeable separation technology. As farmers diversify crops and the type of soil they farm, more demands are put on harvest equipment. Until now, there has not been a practical solution for switching between deflection rollers and finger webs.
ChangeSep, a hydraulically interchangeable separator, has changed that. The technology enables operators to quickly switch between finger web (ClodSep), and deflection rollers (EasySep) from within the cabin of modern Grimme harvesters.
COMING TO AMERICA
Maximilian Gerken, head of marketing, shared news at the show for American potato farmers. Spudnik, he said, will be launching its first self- propelled harvester, TerraTron, at an open house in Idaho in January.
The 4-row, self-driving, 683-horsepower machine has a harvest capacity of over 500 tons/hour.
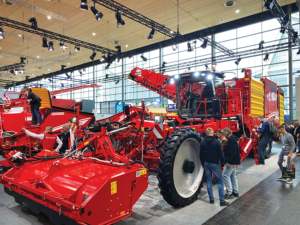
Gerken also highlighted the launch of the third generation of Varitron 470, a 4-row, self-propelled harvester that’s gained interest in North America, particularly among growers who need to harvest smaller potatoes. Varitron 470 offers several upgrades over previous models.
“We optimized the product flow from the intake over the separator to the bunker,” Gerken explained. “We also have more intake options for this machine, so you can use it for carrots and onions, and also for potatoes.”
OTHER ADVANCES
Tolsma-Grisnich introduced a new optimization module under its Vision Control software called Weather in Control. Based on a 10-day weather forecast, Weather in Control makes intelligent decisions around ventilation and refrigeration in storage.
The module’s advantage is maintaining a more precise storage temperature product, and the result is less weight loss and reduced energy costs, explained Jan van Maldegem, farming and marketing manager, Tolsma-Grisnich.
While not specifically designed for potato production, Precision Planting’s Radicle Agronomics is a notable innovation that also received a silver innovation award. The fully automated soil laboratory gives professional agronomists the ability to analyze hundreds of soil samples quickly and accurately.

The lab is supported by a suite of tools that includes GeoPress, a collection module that mounts to the back of a truck or quad. Collected soil is poured into the GeoPress system via a funnel where it’s blended and stored in a reusable tube. The tube is equipped with a Radio Frequency Identification tag that records geolocation as well as additional field data, omitting the need for the previously used bag-and-tag approach.
Back at the shop, the Radicle Lab holds up to 400 samples and produces results, sample by sample, in as little as 15 minutes.
“It can be run by anyone who can run a dishwasher,” said Dale Koch, Radicle Lab product lead.
IDAHO IN THE SPOTLIGHT
Every two years, Grimme and its U.S.- based sister company Spudnik invite 50 of their biggest North American clients to Agritechnica. Among this year’s invitees were three of six Wada Farms farm managers: Todd Jensen, Shane Tilley and Brent Watt.
Wada Farms is a large Idaho-based operation with its own fresh pack facility. Its 30,000 acres of production spans 70 miles. The company has contracts with large-scale processors including McCain’s, Simplot and Lamb Weston.
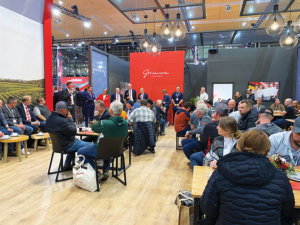
The trip included farm and storage facility tours in some of Europe’s biggest potato-producing countries. It provided the visitors with insight into the difference between European and North American production systems. For all three farm managers, it was their first time visiting Agritechnica.
While most of the equipment the three saw wasn’t large enough for a North American farm, Jensen noted some equipment details piqued his interest.
“There’s a lot of ingenuity that comes from here that gets incorporated into our equipment,” he said, pointing to roller tables.
GLOBAL COMPARISON
The three farm managers were overwhelmed by the sheer size of Agritechnica and amused by the small size of European equipment. Watt said he was amazed by how many companies make virtually the same equipment. He was also impressed by how many tractor brands were present, many of which he’d never seen before.
“In our world, there are only a few options,” he said.
While many of the companies were unknown to the managers, agtech company Lemken was known to all three. Tilley said he’s particularly fond of Lemken’s compact disc harrow, the Rubin 12, as it’s able to operate at high speeds, which is ideal for large-scale operations.
“They make good product, they really do,” said Tilley.
While touring farms, Jensen was surprised by field conditions European farmers have to work in. “I mean, we’ve seen videos today of water standing in the potato rows, and they’re harvesting,” he said. “We wouldn’t even think about that. We wouldn’t even consider it.”
Another eye opener was how regulated European farmers are.
“Sounds like their use of chemicals is really restricted compared to where we’re at,” Jensen said. “I mean, you’ve really got to look at a lot of different tools here when you’re trying to take care of your weed problems.”
Tilley shared his concern that some of those tight regulations might be coming to the U.S.
“Without chemicals, it’s gonna be a challenge,” he said.
The Wada Farms managers expressed concerns about several challenges back home too, including water shortages, labor challenges and high fertilizer and chemical prices. Tilley said Mother Nature is his biggest challenge, while Jensen pointed to rising equipment costs.
“Equipment prices have gone through the roof,” he said.
While the issues they face are no small potatoes, all three said they felt “very lucky” they didn’t have to work under EU conditions.