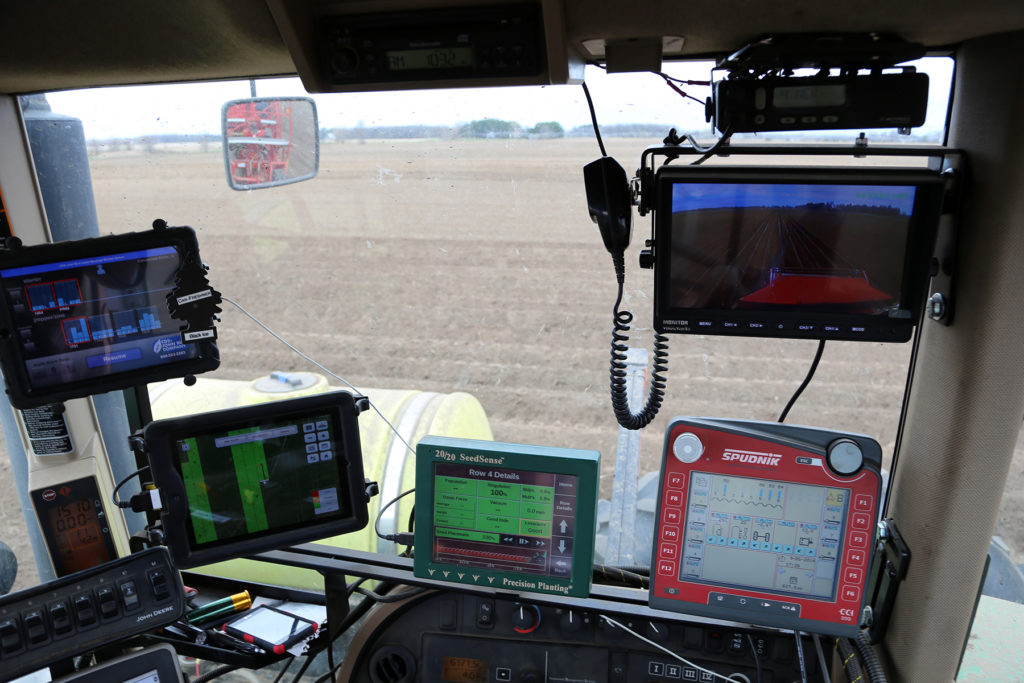
Hot on the Trail
Because potatoes have to be cooked before people consume them, the industry maybe wasn’t as quick to embrace traceability technology and processes with the same urgency as those who grow and process commodities like berries or lettuce.
Not so much anymore.
“The potato industry continues to follow recommended traceability best practices. However, it is not to the level of ready-to-eat vegetables (because) potatoes need to be cooked,” said Dave Masser, president of Pennsylvania-based Sterman Masser. “I think the (potato) industry has followed suit (regarding other commodities). I just don’t know if it’s been as quickly as some other portions of the industry.”
Still, it’s coming along, thanks in part to government regulations and customer expectations.
“In recent years, with the implementation of the Food Safety Modernization Act and advancements in technology, customer expectations have increased focus on product traceability,” said John Lynch, national quality assurance manager at RPE Inc., a national distributor of potatoes and onions. RPE is headquartered in Bancroft, Wisconsin, where it partners with Wysocki Produce Farm, Paragon Produce Farms and a national network of growers and packaging operations to source 10 million CWT of potatoes annually.
In fact, making sure that potatoes are traceable from farm to plate is as important as with any other commodity, said Idaho Potato Commission Vice President, Legal and Government Affairs Patrick Kole.
“A lot of it is basic economics in the sense that if you have a particular problem, you want to isolate and contain that problem so you don’t end up having to recall or destroy any more of the product than is necessary to assure food safety,” Kole said.
There’s another angle, too, he said, and that is to combat food fraud.
“What you want to try and do there is make sure if someone is putting a product into the marketplace and labeling it as an Idaho potato or Vidalia onion, that it actually is – that it came from that spot,” Kole said.
A variety of technologies and systems are used by potato growers, packers, shippers and processors to track product. Kole said that Idaho Potato Commission and state industry leaders have been participating in an initiative known as PSO, or producesupply.org.
“It’s basically a group of people who work at different types of produce companies who evaluate and look at all of the different technologies that have been developed or are being developed, to see what is most cost effective for the potato industry,” Kole said.
Potatoes can present their own challenges because of the volume and ways they are shipped and sold. The sheer variety of ways potato are sold can be daunting; for example, traditional and specialty varieties in bulk, in various sizes of bags, in trays – even a single potato shrink-wrapped and microwave ready.
“When you have bins of potatoes in stores, you have a little bit of a unique problem because a lot of those bins can be reused,” Kole said. “You can lose that product integrity, that identity integrity. But at the root of it, the core is the same: making sure you can trace and detect and show that the product is from this one particular (lot).
“I think the industry is doing a really good job when you look at what we see in the marketplace. You don’t see a lot of consumer confusion and we don’t see a lot of recall activities.”
VARIETY OF APPROACHES
How companies arrive at those results varies, however.
Lynch says that RPE’s growers and packaging operations track every step: from seed sourcing to planting, cultivation, harvesting, storage and packaging. It’s a complex process, given that the company sources multiple varieties from Wisconsin, Michigan, Colorado, Idaho, California, Washington and other states.
“RPE overlays distribution in providing complete traceability for our customers,” Lynch said. “A dataset is created for every process step from seed to customer delivery.
“We must be able to accurately align and report each of the datasets for any individual lot of product.”
RPE Food Safety Manager Kristen Granger says technology to support traceability is key to continued progress.
“Technology has advanced, but tracking our products still involves consolidating information from multiple software systems and datasets,” she said. “Our ability to track our products has a developed with the technology, but it will continue to improve as more integration between our systems becomes possible.”
Wendy Alsum-Dykstra is in charge of PTI (the Product Traceability Initiative) at her family’s Alsum Farms & Produce in Friesland, Wisconsin, a grower-packer-shipper of potatoes along with other operations. In 2017, Alsum Farms planted nearly 2,400 acres of potatoes and sold 2 million hundred weight of potatoes.
She said their traceability system is designed to meet customer requirements, but isn’t fully integrated with other systems.
“We capture the lot information when we receive product in – that lot
information ties back directly to the grower,” she said, explaining that the company’s ERP (enterprise resource planning) system traces produce to the pallet level.
“We use a system called PTI Lite to print case labels. This software along with the company’s ERP system provides complete traceability to meet case labeling as well as reporting requirements.” she said.
Not all of their customers require PTI. But when they do, their hybrid approach has worked.
“We have some customers who annually or semianually require mock recalls,” she said. “We are allotted two hours to provide supporting records to trace from the customer back to the grower and we’ve always been successful.”
Bill Menkveld, vice president of sales and administration for Greentronics in Elmira, Ontario, developed a product called RiteTrace about five years ago that automates data in potato production from field to storage.
“If you have a problem in storage, the first thing you want to know is where did that crop come from?” he said. “Was that a problem that started in the field? Was it too hot? Did the crop quality look OK when it went into the bin and now it isn’t? Was there something I could have done in the field?”
RiteTrace monitors every load – providing such information as field maps and load origins, crop yields, detailed load maps for storage bins or rooms, timing and location of each load, crop and ambient temperatures along the way and more.
“That provides growers with a lot of information – especially big growers with dozens of trucks: how much time everything takes, which trucks take longer than others, how much harvest in a day and where those loads go,” Menkveld said. “That’s really valuable information for growers to manage their farms better.
“And if you do end up with a question about the crop you’re delivering – maybe it’s substandard and there’s an issue with it – now you have a map that you can show to your buyer … that can give your buyer a lot more information.”
Greentronics continues to test new RiteTrace features in actual growing, storage and transport conditions. Menkveld said it’s a work in progress, with new developments coming in response to grower-shipper needs.
Most recently, Greentronics implemented a seed potato tracking feature that tracks seed potatoes from where they come out of storage through transportation to the field and into the planter.
“This allows us to track variety/seed lots and also weight of seed through each planter,” he said, noting that the system was slated for spring 2018 implementation in Idaho.
FROM FIELD TO PLATE
Masser said his company adopted technology from Idaho-based EnvioAg about five years ago. Starting small, Sterman Masser “really started to ramp it up here (with EnvioAg) in the last three years,” he said.
While the company had a traceability process in place before, it was much more labor intensive and manual. Now, he said they use EnvioAg every step of the way – from collecting field data at planting to harvest to tagging crates where potatoes are stored, through purchase and sales orders, processing (Masser offers lines of washed and ready to steam, grill or bake potato products), shipping and delivery.
It’s a complex system, tracking everything from 50-pound cartons to one-pound microwave-ready gourmet specialty potatoes. The company can store about 600,000 cwt. of potatoes in its Pennsylvania facilities.
“We’ve got a wide range of products and varieties and types that we’re running in our facilities – multiple lines, multiple sizes, multiple packs. It’s very complex,” he said. “A lot of our loads leaving here have 15-plus items on the truck.
“So we needed a system robust enough to handle all of that inventory management, scanning and traceability.”
That’s what the company found in EnvioAg, he said.
“We still have to enter data, but now we can trace potatoes in minutes – not hours,” Masser said.
Besides the need for traceability and focus on food safety, the company embraced the system for its capabilities as a management tool. The availability of so much detailed data has aided Masser in helping its growers understand the accounting side of the business.
“Being robust in the technology sector is an important part of the growth of our business, and having a data-rich business means we can pull trends and information and do a better job of forecasting and projecting where our business is going,” Masser said.
Not that food safety isn’t a driving force.
“My position on food safety is that yes, it’s something that our customers and retailers require, but it’s something that we as shippers need to be responsible for,” he said. “We need to be doing the right things for consumers and our business to have protections in place.
“It’s really more along the lines of sustainability and the business responsibility we have to conduct ourselves (in a way) to provide healthy and safe foods.”